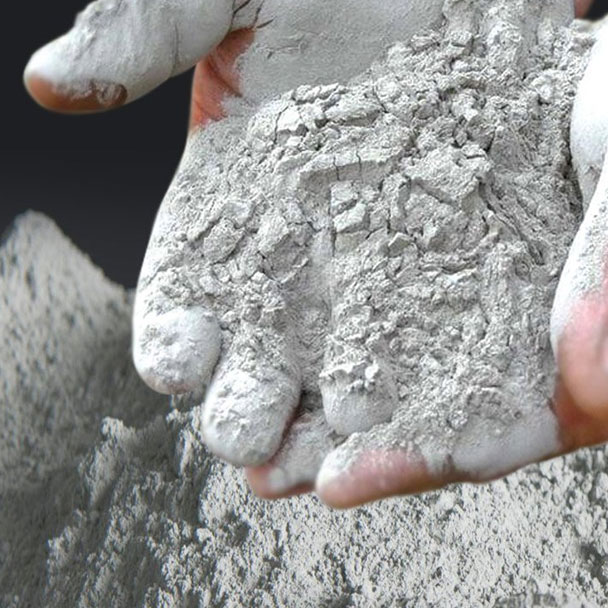
What is GGBS
Pyramid Industry PVT. LTD introduces BUILDCEM Ground Granulated Blast Furnace slag (GGBS) A QUALITY CEMENT extender. BUILDC EM GGBS is suitably processed in well-equipped plant.
BUILDCEM GGBS, is Processed to achieve Optimum particle size distribution to facilitate cementitious contributions when Blended with cement BUILDCEM GGBS goes through Quality checks at Various stages to ensure Satisfactory performance as cement replacement / substitutes. Buildcem Ground Granulated Blastfurnce Slag is used in combination with Portland Cement to produce superior longer lasting concrete.
A replacement rate of up to 50% is permitted by the IS-456 -2019 & IS 10262-2019. Buildcem GGBS replacement greater than 50% is classified as sulfate resistant cement and can be used in aggressive ground conditions.
Buildcem Ground Granulated Blastfurnce Slag is an industrial by-product that is diverted from landfill and upcycled into a commodity product. On exiting the iron processing system, molten blast furnace slag is rapidly quenched with water to form Granulated Blastfurnace Slag (GBS). The GBS is sourced from selected high quality suppliers in India. Buildcem GGBS is produced by drying and grinding the GBS at our manufacturing plant in Wakaner, Nr. Rajkot (Gujarat).
BUILDCEM GGBS is a off - white free flowing powder. It imparts a lighter, brighter color to concrete. in contrast to the stony grey of concrete made with Portland cement. In general, addition of BUILDCEM GGBS improves aesthetics of concrete. BUILDCEM GGBS largely contains high amount of reactive components - calcium alumino silicates.
Reactive Silicates or Glass is mainly responsible for secondary hydration reaction when cement is mixed with BUILDCEM GGBS, facilitates lime |Ca0l. As a result of secondary reaction between lime and reactive silicate, more volume of C-S- H is produced - Key to better performance in concrete made with BUILDCEM GGBS.
Advantages of GGBS

Fire resistance
Structures made with GGBS based concrete resist the high temperature than the structures made with Ordinary Portland cement

Reduced life cycle cost
Concrete produced by using GGBS can significantly improve the durability and extends the life of the structure and thus reduce the lifecycle cost of the structure.

Reduced Permeability
The inter connectivity of capillary pores will be discontinued and thus permeability will be reduced.
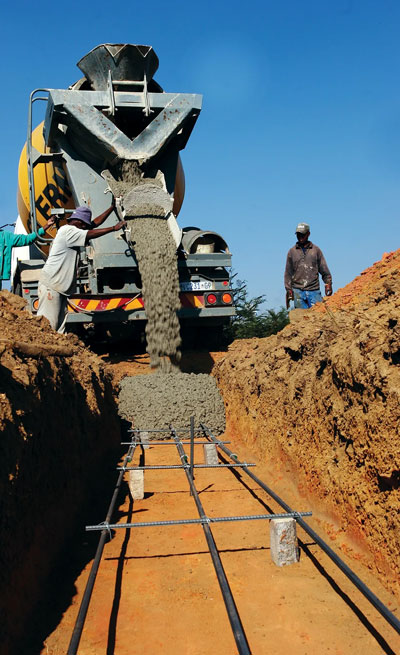

Resistance to chloride attack
Due to reduced permeability and increased densification the diffusion of chloride ions will be greatly minimized in the concrete containing GGBS.

Better Particle packing
Concrete made with GGBS has better particle packing due to particle shape and improved hydration.

Reduced heat of hydration
Due to reduced heat of hydration, plastic shrinkage cracks can be minimized.
Key Attributes of BUILDCEM GGBS
Enhanced Durability (Protection against Sulphate & Chloride attacks)
0ne of Key attribute of use of BUILDCEM GGBS as Part replacement of cement concrete is enhanced duality of concrete. Use of BUILDCEM GGBS leads to reduction of permeability in concrete, as consequence concrete made with BUILDCEM GGBS will offer increased resistance to ingress of harmful elements its such as Chloride, it is particularly important for reinforced concrete used in marine, coastal environments and in road bridgs. Where the concrete is exposed to aggressive environment. This is attained due to reduction of capillaries and small pore diameters in concrete. which makes ti more impermeable to allow e n try of harmful elements.
High Long terms Strength
Concrete Containing BUILDCEM GGBS achieves higher ultimate strength than concrete made with Portland cement. with passage of time, BUILDCEM GGBS also makes cementitious contribution . Its optimum addition in concrete generates more strength -enhancing calcium silicate hydrates |CSH I than concrete made with Portland cemenI only. concrete made with BUILDCEM GGBS continues to gain strength over time. Concrete mix can be suitably proportioned to develop design for a particular strength grade of concrete.
Protection against Carbonation/Corrosion
Over a period of time, in normal concrete, the tendency to absorb atmospheric Carbon dioxide (CO2) resulting in Carbonation. It also affects the alkalinity of the concrete leading to reduction of effectiveness concrete/cement matrix as a protective medium. Concrete with BUILDCEM GGBS maintains sufficient alkalinity; this reduces the chances of carbonation in concrete.
The use of BUILDCEM GGBS is expected to increase the life of the concrete structure as compared to concrete structure made with Portland cement.
Lower Heat and Denser Concrete
BUILDCEM GGBS can be very effectively used to limit the temperature rise in Large Concrete pours / Mass concrete. The more gradual hydration of BUILDCEM GGBS generates both lower peak and less total overall heat than Portland cement. This reduces thermal gradients in the concrete, which prevents the occurrence of micro cracking which can weaken the concrete and reduce its durability.
BUILDCEM GGBS is ideal cement substitute for mass concrete, foundations, dams etc.
Potential Applications for BUILDCEM GGBS
- Foundations, Piles, Underground Structures, Aqua ducts , Canals Culverts and flyovers
- Multi storied building construction.
- Pre-cast concrete
- Mass concreting project works like Dams, Bridges ,Barrages and Canals.
- Concrete Pipes, Precast Tunnel Linings
- Structures in swamp areas and footings, Plinth beams etc.
- Water tanks and other water retaining structures
- Construction in coastal areas and in saline areas where alkali content is more.
- Manufacturing of Cement Based Products such as Grouts, Plaster, Mortars, AAC Blocks, Partition Boards, Cegent Pipes, Roofing Sheets, Solid and Hollow Concrete Blocks and Bricks, Wall putty
Chemical Composition
SiO2 | AI2O3 | Fe2O3 | CaO | MgO | MnO | TiO1 | SO | CI | S2- | Na2O |
---|---|---|---|---|---|---|---|---|---|---|
36 | 12.5* | 1.1 | 36 | 10 | 0.3 | 0.5 | 0.1 | 0.02 | 0.6 | 0.5 |